ENVIRONMENT
We acknowledge that environmental protection and adaptation to climate change is a great opportunity to reshape our operations, aiming to become a positive contributor. Climate-related risk assessment helps us define our strategy, align our investment decisions and adopt our actions, making the most of our operations on a risk-conscious basis.
Material
Issues
Emissions
Energy
Effluents and waste effluents
Biodiversity
Water and effluents
Waste
Goals
2021-2025
Status:
13 out of 21
environmental goals for 2025
have been already embedded
in 2024.
SDGs
Climate-Related Risks and Policies
When it comes to climate change, we recognize the necessity of following the recommendations of the Task Force on Climate-related Financial Disclosures (TCFD) to categorize, manage and report on climate-related risks of both categories (physical and transition).
Our commitment is net zero GHG emissions by 2050, pursuing efforts to be net zero earlier-subject to technology and shipyards’ slot availability. In Danaos, we have implemented numerous energy-efficiency measures and developed tools, such as an Internal Carbon Pricing mechanism to evaluate and mitigate environmental impact. We align our disclosures with Task Force on Climate-related Financial Disclosures (TCFD) framework to provide stakeholders with clear insights into our climate-related strategies and risk-management practices.
Having considered climate change scenarios SSP1- 2.6 and RCP 8.5, Danaos invested in automated systems for advanced sea routing and passage plan control, which have been installed to company vessels and at the same time, we invested in a software for advanced mooring force calculation and employee training, so as to ensure safe operation for vessels at port.
In the meantime, we are monitoring developments in the field and waiting for the International Association of Classification Societies (IACS) to adopt new, upgraded structural rules for newbuilding vessels. In addition, following the damages that our major lubricant and additive suppliers sustained due to their hurricane-damaged product berths and the consequent shortage in supply that could result in disruption of vessel operation, we adapted our consumables management policy by optimizing the supplied quantities to our vessels. We also devised a smart monitoring and alerting system via our WAVES data analytics platform so that the necessary quantities are always kept onboard to guarantee vessel safe operation. Furthermore, we have diversified our suppliers and supply ports to have alternative supply options. Finally, as a measure to deal with prolonged stays at anchorage owed to extreme weather conditions (i.e. coastal flood, heavy wind, thunderstorms) that
may impact and terminal infrastructure and result in physical climate disruption, we have invested in the application of top low friction paints that guarantee longer idling periods while adjusting our provisions management policy accordingly.
Our supply chain resilience and consumables management adaptation, along with the supplier’s diversification strategy aligns well with industry best practices in climate-driven supply chain risk mitigation.
Our Head office building is our key land – based asset. This is at low risk for physical impact of climate change and disruption of operations. A mitigation solution tailored to the scenario of total destruction entails a back-up land-based infrastructure established in another country, while, in case that that the approach to the Head Office premises is blocked by whatever reason, remote operation is feasible and well-tested during COVID-19 pandemic period. Our business continuity strategy aligns with industry best practices, particularly in risk management for corporate infrastructure.
Danaos’ decarbonization path, as per LCTP, goes through an extensive optimization plan for improved operational efficiency on existing fleet, as well as 2nd-hand ECO vessel acquisition and a NB-vessel program with ECO vessel ready to accommodate green fuels in the future, with already six (6) green newbuilding vessels delivered in 2024, as well as sixteen (16) green newbuilding vessels under construction to be delivered in the period 2025-2028. We estimate that the very ambitious scenario SS91-1.9 will prevail with the 1.5oC objective of the Paris Agreement, which is why we are trying to identify ways to align our targets with SBTi targets, despite hindrances that need to be overcome.
LCTP addresses IMO targets following IEA SDS pursuing efforts to meet the stricter 1.5oC Paris Agreement goal.
In Danaos we decided to strengthen decarbonization policy, setting new stricter targets of 50% carbon intensity reduction by 2030 compared to 2008 levels, with the aim to net zero GHG emissions by 2050.
LCTP addresses IMO targets following IEA SDS pursuing efforts to meet the stricter 1.5oC Paris Agreement goal.
Our LCTP articulates the main aspects of our environmental strategy in:
- Maximizing the efficiency of the existing fleet: Our investment in energy efficiency and Internal Carbon Pricing (ICP) tools demonstrates a strategic approach to emissions reduction and cost optimization. These tools enhance data- driven decision-making and sustainability impact assessments. Recognizing the limitations of energy efficiency improvements on the existing fleet underscores the importance of fleet renewal and exploring alternative fuels.
- Cooperating closely with our clients on a transparent data-sharing basis aiming to optimize the vessel trade route through an advanced leg analysis methodology, developed in-house.
- Working on the prevention of power penalty development through advanced performance monitoring tools: We try to achieve the maximum engagement of our people in this process. By emphasizing real-time performance evaluation and proactive corrective actions, we’re ensuring both operational efficiency and long-term sustainability. In this respect, we invest in advanced performance- monitoring tools, crew engagement and training on energy efficiency best practices, while we encourage a data-driven culture where crew actively contributes to performance monitoring.
- Green fuel readiness and fleet renewal, ensuring Danaos is well prepared for the maritime energy transition.
In Danaos we decided to strengthen decarbonization policy, setting new stricter targets of 50% carbon intensity reduction by 2030 compared to 2008 levels, with the aim to net zero GHG emissions by 2050.
In the scope of DANAOS disclosure about the application of TCFD framework in the management of climate-related risks, a comprehensive TCFD-aligned gap analysis was performed. In Danaos, we have assessed climate-related risks, identified their potential impacts and developed response mechanisms to mitigate these challenges.
These risks are categorized in transition risks (policy and legal, technology, market and reputation) and physical risks (acute and chronic climate impacts).
In connection to regulatory and policy risks pertinent to EU ETS, Fuel EU Maritime and IMO CII potential penalizing related increased operating costs, Danaos ensures compliance through data transparency, emission tracking and fleet efficiency upgrades. Danaos deals with technology risks by investing in fleet renewal, digitalization and fuel -flexibility to mitigate obsolescence risks.
The answer to increased scrutiny from investors, regulators and customers regarding sustainability commitments is Danaos transparent ESG disclosures (CDP, CSA, GRI, SASB) and the issuance of an annual Low Carbon Transition Plan. When it comes to acute physical risks, Danaos utilizes advanced weather routing, automated passage planning and risk-based fleet deployment.
Response to chronic risks entails Danaos integrating climate resilience planning in asset management and exploring adaptive technologies.
We have also identified climate-related opportunities, evaluated their potential financial impact and developed a strategy to capitalize on them.
More specifically, in terms of resource efficiency, our strategy includes continuous investment in energy-saving solutions, digital monitoring and operational optimization. The growing customer demand for low-carbon shipping solutions is addressed through transparent emissions tracking and active collaboration with our clients. The low-carbon transition and fuel innovation requires investment in eco-vessels ready to undergo “green” retrofit, while we continuously enhance our risk management frameworks and integrate climate scenarios in our strategic planning.
A detailed description of the identified risks, their potential financial impact and the corresponding response strategies, as well as the opportunities, their financial implications and the approach to realizing them are thoroughly documented in Danaos’ CDP report. This comprehensive disclosure ensures transparency and aligns with best practices in climate risk management.
Emissions
Regulatory Framework in Shipping on Emissions Reduction
The regulatory framework for emission reduction in shipping has been evolving, with international, regional and national regulations aiming to curb greenhouse gas emissions and improve the sustainability of the shipping industry. The key frameworks and regulations for 2024 are mainly associated with short-term decarbonization measures to reduce CO2 emissions, including Energy Efficiency Existing Ship Index (EEXI) and Carbon Intensity Indicator (CII) and looking into alternative fuels like ammonia, hydrogen and biofuels, as well as wind and solar propulsion systems as a means to achieving net-zero emissions by 2050.
The EU has been at the forefront of regulating emissions from the shipping industry through various mechanisms, including the enforcement of EU Emissions Trading System (ETS) since 2024. With this system, shipping companies must buy allowances to cover their CO2 emissions, serving hence as a financial incentive to reduce emissions, to promote measures to reduce greenhouse gas emissions by 55% by 2030 (Fit for 55 Package) and to incentivize the use of alternative energy sources (biofuels etc.).
Various countries have enacted their own regulations or are introducing stricter measures, particularly in their coastal and inland waters, such as emission caps, low-sulfur fuel requirements and stricter enforcement of emissions from ships. In the U.S., the California Air Resources Board (CARB) enforces strict air quality standards for ships operating in California’s waters.
While the regulatory framework has made significant progress, challenges remain in achieving ambitious decarbonization goals, including primarily fuel availability and infrastructure – since the production and distribution of alternative fuels are still in the early stages- and substantial investments are still required, along with significant technological costs and operational impacts. There is a continued shift towards cleaner technologies, but the path to full decarbonization will require ongoing innovation and collaboration within the shipping sector.
Fighting Climate Change
Our company embraces IMO’s vision and its revised targets as set through the latest MEPC and works towards solid proposals for their improvement. In Danaos, we have developed online tools for monitoring the emissions of the vessels on a real-time basis, enabling a first benchmarking of Fuel EU compliance and arising costs and risks. The RED-II supports the development of renewable energy across the continent, serving as a turn point for the production of e-fuels and reduction of their production cost and making large scale production feasible and viable. Another EU action related to the ESG framework, also declared as pivotal towards carbon economy, is the introduction of EU Taxonomy with the aim to classify investment in an environmental sustainability scale, by codifying the Green Bond Principles.
Heading Towards Decarbonisation
The shipping sector is undergoing a “third revolution” driven by decarbonization, regulatory evolution and alternative fuels. This transformation is fuelled by: regulatory updates, alternative fuels and new technologies and digitalization and AI driven efficiency solutions that reshape operations.
In the fast-evolving maritime industry, standing still is not an option. With regulatory shifts, alternative fuel innovations and decarbonization pressures, companies must continuously adapt or risk falling behind.
To meet our goals, the entire industry should embrace a mentality as expressed in a phrase of Johann Wolfgang von Goethe:
“He who moves not forward, goes backward.”
NASA’s MODIS satellite instrument reveals how air pollution may alter clouds, affecting global temperatures (area in Pacific Ocean).
This visualization illustrates the effect by showing how ship exhaust leaves brights cloud trails in clean ocean air.
Following the roadmap outlined in the Low Carbon Transition Plan (LCTP), the company aims to seize opportunities for further business development by investing in ships that are commercially attractive with a low carbon footprint. In alignment with the International Energy Agency’s (IEA) Beyond 2˚ Scenario (B2DS) analysis, Danaos has decided to bolster its decarbonization policy by setting more stringent targets. These targets include a 50% reduction in carbon intensity by 2030 compared to 2008 levels, with the ultimate aim of achieving net zero GHG emissions by 2050.
We embarked on a comprehensive Low Carbon Transition Plan (LCTP) aimed at reducing emissions from our fleet. In the short term (2022-2024), we prioritized retrofitting the fleet. More than 225 installations took place on our vessels, spading from propulsion improvement to navigation upgrades and M/E tunings.
Medium-term opportunities (1-3 years) to reduce emissions from fossil fuels were explored. We committed to applying Alternative Marine Power (AMP) arrangements to 25% of our fleet by 2025, with a focus on supporting decarbonization at ports, especially those subject to regulations on on-shore power.
Additionally, the company investigated biofuel as an alternative fuel, recognizing its potential to lower greenhouse gas (GHG) emissions, particularly considering its technological readiness and near-term availability. Following the IMO MEPC 78 outcome in 2022 regarding simplifications on the use of biofuels with contents up to 30% (B30), Danaos has actively participated in its charterer campaign, successfully supplying five vessels with 10 bunkerings of biofuel blends (B30 and B24) with almost of all them being certified as sustainable biofuels by the certification schemes (ISCC, RSB, EU REDII cert).
The most significant concern when the conversation comes to biofuels is the biomass feedstock the fuels is produced from. The demand for biofuels is expecting a boom during the years to follow and, to avoid adverse effects in social and environmental areas, selection of feedstock should be treated with due diligence.
In addition, Danaos has become a member of the Ammonia Energy Association to keep up with all developments in relation to methanol and ammonia use in the maritime industry.
Looking towards the long term, Danaos adopted a strategy of divesting from older technology vessels and acquiring new vessels with advanced environmental features. The company set standards for new builds, prioritizing vessels with ECO designs, Methanol-Ready capabilities and Cold Ironing plants. Already, Danaos has sixteen green newbuilding vessels under construction, scheduled for delivery between 2025 and 2028. All our newbuilds in China will be methanol ready, while nine of them will hold ammonia-ready notation as well.
We adopted a diversification policy of Danaos portfolio and, in 2024, we expanded further our operation in dry bulk sector with the acquisition of three (3) additional Capesize carriers leading to ten (10) Capsize bulk carriers in our fleet in total. Studies on how to convert these carriers into more efficiently operating vessels have already begun, while some relevant to propulsion improvements are already in implementation phase.
Engagement with suppliers was also crucial in Danaos’ decarbonization journey. The company promoted awareness, incentivized emissions reductions and engaged with partners across the value chain, setting criteria for ESG performance. Danaos also recognized the importance of stakeholder engagement in achieving its decarbonization goals. Through its membership in industry associations such as the Global Maritime Forum (GMF), Danaos adhered to the Getting to Zero Coalition statement, aiming for net-zero emissions by 2050. The company also maintained contact with Science Based Targets (SBTi), actively monitoring developments in the finalization of science-based tools tailored for the shipping industry. The collaboration with stakeholders, including financial institutions, industry associations and suppliers, was essential in navigating the challenges of decarbonization and ensuring a sustainable future for the maritime industry.
We adopted a diversification policy of Danaos portfolio and, in 2024, we expanded further our operation in dry bulk sector with the acquisition of three (3) additional Capesize carriers.
Going one step further to fight climate change, Danaos introduced in 2022 carbon offsetting by neutralizing the Headquarters’ carbon footprint including employees commuting emissions, with the aim to balance unavoidable emissions. The carbon offsetting that was verified by a third party, is a proactive action outside our value chains to contribute towards decarbonization and is beyond our near-term and long- term targets set.
Last but not least, in 2024 we enrolled in Voluntary Carbon Market, where savings from retrofits are translated in carbon credits. Enrolment in a program compliant with Gold Standards has been thoroughly investigated during the previous years for all retrofitted vessels and was finally contracted within 2024. In total, thirty (30) retrofitted vessels were enrolled with the aim that relevant income from carbon credits to be directed to investments for fleet renewal and environmental upgrade of our performance. There is a link between green performance and VCM, since funds anticipated for large scale retrofits will provide capital for ship-owing companies, making decisions for retrofits and green fuels more viable.
We have also performed speed trials to verify new speed power curves on both vessels retrofitted with propulsion improvements, as well as on vessels retrofitted with new propellers or ESDs.
In 2024 we enrolled in Voluntary Carbon Market, where savings from retrofits are translated in carbon credits.
Emissions Reduction
We have developed an advanced monitoring tool for the fleet’s emissions to evaluate and monitor energy efficiency. Danaos calculates the emissions of the entire fleet, to ensure transparency and emissions management. These metrics are indicators of environmental performance and are shared with clients, upon request, so that they can in turn evaluate their environmental footprint (value chain footprint – Scope 3 GHG protocol).
The regulations on carbon intensity in place since 2023, which contributed to the significant impact on operation and vessel speed reduction in the previous year and the introduction of EU ETS directive in 2024 encouraged shipping companies to adopt slower speeds or optimize their operations to reduce emissions. As a result, this year there were no significant changes to the ship’s operations compared with the previous year, to remain in compliance with new requirements.
More specifically, following the significant speed drop by 1 kn in 2023 compared to 2022, the fleet’s operation followed the same pattern. As a result, the average speed in 2024 remained steady at 14.7 kn compared to 2023 and fleet average draft was 11.2 m in 2024, compared to avg draft 10.7 m in 2023.
In 2024, we successfully achieved our stricter goal, compared to IMO, for 50% reduction in CO2 emissions intensity by 2030 (baseline 2008 IMO) (grCO2/tones* miles) 6 years earlier than the target!
The extensive retrofit plan which was initiated by Danaos in 2023 and continued in 2024, aiming at enhancing vessel energy efficiency, coupled with speed reduction initiatives, was reflected in the Energy Efficiency Operational Indicator (EEOI), which dropped at 13.26 grams per ton per nautical mile in 2024, compared to 14.05 gr per ton per nautical mile in 2023. This achievement signifies a substantial environmental milestone, marking a 51.4% reduction in CO2 emissions intensity when compared to the 2008 baseline. This kind of progress shows a strong commitment to sustainability and the reduction of carbon footprints, which is crucial when addressing climate change. Achieving such a reduction involves a combination of improving energy efficiency and adopting cleaner technologies and it sets an excellent example in industry efforts to work towards a greener future.
This kind of progress shows a strong commitment to sustainability and the reduction of carbon footprints, which is crucial when addressing climate change. Achieving such a reduction involves a combination of improving energy efficiency and adopting cleaner technologies and it sets an excellent example in industry efforts to work towards a greener future.
The formula used for the calculation of our emission KPIs are in line with the ones used by the KPI platform: https://www.shipping-kpi.org/. We adopted this approach so as to use the same reference tool as that of our charterers and be fully aligned. After successful implementation of the IMO Sulphur cap 0.5% back in 2020, along with currently 9 existing vessels with open-loop scrubbers’ installation and another six newbuilding vessels that were delivered in 2024 and two 2nd-hand bulk carriers delivered in 2024 also fitted with SOx Scrubber, Danaos has been closely monitoring Sulphur and nitrogen oxides to be able to measure our impact into the atmosphere. In addition, the fourteen of our sixteen newbuildings will be SOx scrubber-fitted and will also incorporating NOx emission reduction technology for Tier III compliance (SCR, EGR). R&D is constantly studying new technologies to identify the best fit for the fleet and the environment.
For the scrubber fitted vessels, aiming to accurately calculate the SOx emissions, we receive the data directly from emissions monitoring sensor. In this way it is possible having in our online platform the exact Sulphur calculation. We have also implemented in our systems the monitoring of both air emissions and wash-water discharged at sea, in order to timely identify and respectively rectify any potential malfunction and minimize violations.
Significant improvement reflected in the data above is achieved through various optimization strategies and retrofits. It is estimated that, for these Low Carbon Products (based on provided data of fuel savings from makers), which are being monitored for their reliability via Waves, the fuel consumption would be by 5% lower from the consumption if these modifications and actions had not been carried out.
Moreover, Danaos has implemented the installation of AMP in order to contribute to the reduction of emissions of ships while at berth.
In 2024, the target related with AMP installations was achieved, as twelve additional vessels are equipped with AMP, including the six NBs vessels that were delivered in 2024. In total 39% of Danaos’ container vessels is already fitted with AMPs in 2024 and 34.5% of total fleet including bulkers is fitted with AMP in 2024. Our target was to have 25% of the fleet equipped with AMP by 2025.
Danaos has implemented in its core strategy the installation of AMP in order to contribute to the reduction of emissions of ships while at berth.
Emissions Monitoring
The development of a sophisticated environmental routine that will incorporate an interactive Carbon Intensity Index calculation, vessel rating and projection of emitted CO2 has set the foundation for effectively responding to a potential emission-trading or levy scheme that has been launched in Europe this year and is also a potential future IMO regulation.
Close monitoring of SOx scrubbers already installed on existing vessels since 2019 is ongoing through our Waves data analytics platform along with reference logs, ensuring continuous compliance with relevant regulations. We also monitor closely regions that ban the open loop scrubbers to update our monitoring map accordingly.
Scope 1 (Direct) – Scope 2 (Indirect) – Scope 3 GHG Emissions
We calculate our direct emissions (Scope 1) and indirect emissions from purchased electricity (Scope 2) and allocate these per client, while we are currently working on expanding the collection from the value chain GHG (Scope 3) emissions related to our business activity.
Scope 1 CO2 emissions are produced from our ships’ operation, the majority of which takes place at international waters, while Scope 2 emissions are calculated based on a market-based method using residual mix – regional emissions factor.
In 2024, our Scope 2 emissions were reduced by 16% compared to the previous year.
The procedure for Scope 3 emissions has been established and includes suppliers/partners reporting of their Scope 1 and 2 emissions allocated to Danaos. More precisely, the Scope 3 emissions categories include carbon emissions information from traveling agents and our Wellto- Tank (WtT) emissions calculation which relies on the GLEC (Global Logistics Emissions Council Framework) emission factors for the CO2e values. Moreover, Scope 3 categories have been expanded as the company has collected accurate emissions data from courier service companies, to estimate emissions of sending goods onboard through procurement activities, while since 2023 we report shipyard shore power during drydockings and supplier Scope 3 emissions collection
through ESG Questionnaire recorded in Danaos Analytics Platform, which aims to support and incentivize the procurement circle.
More specifically, our R&D department, in cooperation with our Procurement department, has created an Emissions Recording platform in Beyond WAVES environment, where partners are requested to report not only their Scope 1 and 2 emissions related to Danaos involvement and activities, but all ESG aspects that are considered important for sustainable business, addressing in parallel the emissions carbon reporting. The company has set prerequisite and mandatory criteria, mainly related to people and secondary ones related to GHG emissions. A number of KPIs have been introduced in order to follow up partner engagement status. Carbon emissions recording is done in Beyond WAVES platform. Our aim is to assess and measure sustainability activity and ensure the sustainable and efficient performance of our supply chain in compliance with our requirements and standards, which is necessary for creating positive value.
Our “Emissions Allocation” function devised in our Waves platform allocates our Scope 1 emissions on a client/vessel basis, so that our clients can in turn evaluate the size of their contribution in a holistic approach, as a part of the value-chain environmental footprint and thus refine their strategy accordingly.
Below you may find Danaos Scope 1, Scope 2 and Scope 3 emissions for the year 2024.
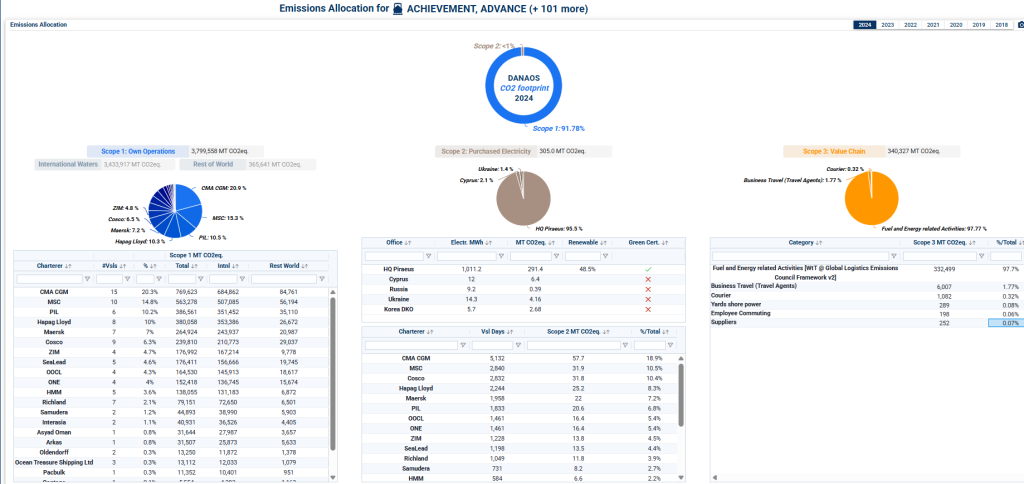
Ozone Depleting Substances
We have incorporated the modifications from the old systems to the new ones and, according to the regulations, any deliberate emission of ODS is prohibited. For new building vessels, any installation containing ODS, such as halons and chlorofluorocarbons (CFCs), is prohibited. The Freon Types in use are R-404A, R-410, R-417 and R-407C. Total Freon Capacity increased in 2024 due to the increase in the number of vessels from 73 in 2023 to 81 within 2024. Freon losses for 2024 were at 10.5% of the total capacity (3,132 kg approximately), reflecting that our efforts to reduce losses are paying off.
We plan to reduce greenhouse gas emissions and mitigate climate change, based on EU F-gas Regulation (517/2014) adopted 1 Jan 2015 for reduction of use of HFCs. A service ban on HFCs with high Global Warming Potential (GWP >2,500) like R-404A, R-507 and R-422D has been imposed since 1 Jan 2020. The F-gas regulation applies to all EU countries and EU flagged vessels. Therefore, replenishment of retrofit of systems with lower GWP refrigerants takes place where required.
Energy
Energy Consumption
Our R&D department has extensively investigated options for minimizing transportation costs and the subsequent fuel consumption required per cargo transferred. This includes optimizing the vessels’ design and operating profile and consequently monitoring performance. More than that, the R&D department is working on a series of alternative fuels such as LNG, methanol, ammonia and hydrogen.
We report on the fleet energy consumption on an annual basis. Fuel consumption encompasses fossil energy consumed/combusted at Danaos operated vessels and infrastructures. Total energy consumption increased by 16% in 2024 compared to 2023. There are no significant consumptions of energy outside the organization that Danaos operations contribute to.
Our R&D department has extensively investigated options for minimizing transportation costs and the subsequent fuel consumption required per cargo transferred.
Headquarters Energy
New buildings
Sixteen (16) new building vessels are under construction and are scheduled for delivery between 2025 and 2028. All sixteen of our newbuilds in China will be methanol-ready, while nine of them will hold ammonia-ready notation as well.
Fuel Consumption
Danaos is compliant with ISO-50001 Environmental Management System adopted in 2015. To achieve decarbonization big money needs to be invested from the sector.
The R&D Department in Danaos monitors all matters related to climate change aiming for energy efficiency improvement onboard and formulates relevant KPIs to ensure compliance with regulations. More specifically, in Danaos we have been working on evaluating vessel performance and examining measures to increase energy efficiency and improve Carbon Intensity Indicator (CII) rating.
On top of the above and as a part of our effort to achieve optimum CII results for our fleet, numerous retrofits have taken place within 2024 as depicted in below graph:
Energy Efficiency measures and initiatives to improve CII
Within 2024, we completed 14 propeller retrofits in our container fleet, 12 out of which fitted with propeller BTF. All above investments are of course distributed in different implementation periods throughout 2024 and various retrofits were carried out on different vessels with various operational profiles. From the investment in the aforementioned low carbon products and enhancements, we have concluded to a fleet weighted average of 5% savings in fuel consumption per vessel.
Apart from being a leading company in containership sector, we have diversified our operation in dry bulk sector with the acquisition of three additional Capesize carriers delivered within 2024, increasing the number of bulk carriers to ten (10) in total.
Technical optimizations and retrofits are being implemented for the second-hand Capesize Bulk Carriers acquired, which are not green-ECO vessels and need to be further optimized, aiming to performance improvement and emission reduction. In 2024, we completed 7 ESD installations (PSV, HVAF and propeller trimming) on the 7 bulk carriers and 2 more vessels remain to be completed with 2025, while one vessel was delivered with the ESD installed. Compliance with Rightship standards and aiming to achieve good fleet rating scores refers to energy optimizations as well, apart from safety aspects.
We remain in compliance with our Low Friction Paint Campaign, with nine (9) vessels with Low friction paints. These measures were complemented by optimization efforts in ship loading and steering, leading to significant power savings and subsequent reductions in carbon emissions. In anticipations of regulatory changes, Danaos prepared for the inclusion in the EU Emissions Trading System (ETS), which is expected to further drive down vessels’ speed.
Waste Management
Circular Economy and Responsible Waste Management
Danaos Electrical Department launched the ReNAV campaign/scheme with the purpose of upcycling old navigation and communication equipment. Our fleet has many sister vessels and equipment is often similar between vessels. ReNAV re-utilizes old equipment or spare parts, thus extending life cycles and reducing environmental impact. When a retrofit is performed, the components removed are assessed and, if unaffected by the fault that caused the need for retrofit, they are dispatched to another vessel or collected in the office as spares for future use. Marine type monitors, processor cards and satellite communication systems are often part of the ReNAV scheme. Parts or equipment cannot be re-utilized in any way are stripped down to basic components (batteries, bare metal parts like frames etc., electronic components) and delivered for recycling.
Danaos Electrical Department launched the ReNAV campaign/scheme with the purpose of upcycling old navigation and communication equipment. Our fleet has many sister vessels and equipment is often similar between vessels. ReNAV re-utilizes old equipment or spare parts, thus extending life cycles and reducing environmental impact. When a retrofit is performed, the components removed are assessed and, if unaffected by the fault that caused the need for retrofit, they are dispatched to another vessel or collected in the office as spares for future use. Marine type monitors, processor cards and satellite communication systems are often part of the ReNAV scheme. Parts or equipment cannot be re-utilized in any way are stripped down to basic components (batteries, bare metal parts like frames etc., electronic components) and delivered for recycling.
Through the ReNAV campaign within 2024, a total of 69 systems have been recycled, 29 systems have been upcycled (have been retrofitted and kept in office stock or sent to other vessels for reuse) and 3 systems have been repaired.
Stepping on with further recycling action in 2024, we have continued the Moorings Recycling Campaign, with two vessels engaged and offloading ropes and coils for recycling purposes, for which certification of collection has been provided by relevant facilities.
ReNav re-utilizes old equipment or spare parts, thus extending life cycles and reducing environmental impact.
Ship Recycling – Handling of Hazardous Materials
We pay special attention to accurate recording of hazardous materials, ensuring smooth cooperation with our suppliers, safe recycling of vessels at the end of their life and selecting recycling facilities which embody safer practices. Since 2017, Danaos has been training its own Quality Control Engineers, as “Hazmat Experts” (currently approved by two Classification Societies: KR & DNV). Danaos’ Quality Control Engineers have proceeded with sampling and the preparation of Inventories of Hazardous Materials (IHM) for over 98% of the entire Fleet, acting proactively throughout the years for certification of all Danaos Fleet.
Within 2024, IHM manuals have been prepared for 5 additional vessels recently acquired in order all Danaos Fleet to comply with current Regulations, being also proactive in the ratification of Hong Kong Convention that will enter into force in mid- 2025.
Overall, from a diversified fleet of 71 containerships and 10 bulk carriers, almost 99% hold an IHM Certificate. 1 vessel remains for certification that will be completed on early 2025. The majority of the vessels have been completed in order to comply with the EU Regulation when entered into force.
Waste Onboard Management
Garbage segregation takes place onboard as part of the DSMS – Safety Management and pollution prevention procedures. We encourage preventing, reducing, recycling, reusing and minimizing waste streams, including garbage generated on board. We provide separate waste streams at the point of collection, so that garbage can be separated and discharged ashore more effectively.
Waste from ships is delivered to waste collectors at various ports and then is discharged according to local regulations regarding re-cycling and disposal, which are unknown to us. It is the company’s policy to separate waste both onboard and ashore, so that can be ready for recycling. Waste streams on board can be divided into two main categories: liquids and solids. Both are controlled, grouped in specific categories and disposed according to MARPOL (International Convention for the Prevention of Pollution from Ships). Operational waste includes those in solid form, which are related to the ship’s maintenance. Some are disposed ashore for recycling i.e., metallic parts and others, such as oily rags (which are non-recyclable), are incinerated onboard to reduce the volume of waste ending up at the landfills.
In compliance with the regulations, ash is collected, retained onboard and discharged at port reception facilities, to be further used as raw material in the construction industry. In 2023, the total amount of ash disposed ashore was recorded as part of our systematic reporting and is shown below. Other waste generated from the living spaces is segregated in categories and disposed ashore for recycling. Waste that is categorized as Hazardous and Medical is carefully segregated, clearly labelled and disposed ashore according to international and national regulations. Two sub-categories of operational waste, which are totally separated as Hazardous, consist of jerrycans & paint cans, for which special care is provided to minimize to the extent possible the remnants of paint/chemical contained. In 2024, we continued recording the quantities of these two items separately from other operational waste, to ensure safe disposal.
As part of our efforts to minimize ship-generated garbage, we endeavor to receive as little packaging as possible on board our ships. Towards this direction, we have agreed with our approved ship-chandlers on a number of practices such as:
The total waste volumes produced onboard per DWT between 2023-2024 are available in the table below:
In 2024, garbage compactors were installed on another 26 vessels of our fleet, bringing the total number of ships that operate compactors to fifty (50). By the end of 2024, 61.7% of the fleet has already been equipped with compactors, with installed units reaching 70% of the container fleet.
As part of the 3R program, our intention is to install compactors in all company vessels by 2025 and thus reduce the waste volume onboard by 50%. In 2024, the total produced quantity of plastic waste onboard was 2,556.99 m3 compared to 2,336.33m3 in the previous year, showing an increase of 9% due to fleet increase, while the quantity disposed for recycling increased by 12.5% compared to 2023, proving sustainability improvement since the ratio of recycling remains above the ratio of the quantity produced.
As part of the 3R program, our intention is to install compactors in all company vessels by 2025 and thus reduce the waste volume onboard by 50%.
The liquid waste category includes mostly oil residues (sludge) produced by the operation of ship main engine and other auxiliary machinery, resulting from the purification of oil. The amount of sludge generated is proportional to the fuel consumed onboard. By analyzing the quality of fuels in specialized laboratories and the constant maintenance of purification machinery, we ensure the minimum quantity of fuel residues.
For the year 2024, the produced quantity of sludge is 19,248.9 m3. Sludge is disposed to shore reception facilities, where after special treatment, it is used further in industrial processes.
All fleet vessels follow a specific Garbage & Sewage Management Plan (GSMP), while a Garbage Record Book and placards for the familiarization of crew and visitors regarding the proper handling of garbage on board are available. Shipboard personnel are trained in the procedures outlined in GSMP and this is recorded. Vessels are controlled for their compliance through audits and Port State Control inspections or local port agencies.
Onshore Waste Management
In parallel with shipboard management, we continuously strive to improve the management of waste generated in our headquarters. As part of our Environmental Action Plan, we monitor the average paper consumption per employee per day and we always encourage our people to reduce paper consumption. Although the number of our personnel increased in 2024, the efforts for less paper use were noted. In 2024, a drop in total paper consumption reached 13.3% per person, compared to 15.8% reduction in 2023.
At the same time, e-waste generation is of major concern. Danaos invests in high-end data and networking electronic equipment, attaining information security and prolonged life cycles. Any obsolete equipment, classified as e-waste, can either be in working condition or be unusable. IT equipment that remains in working condition after it has been data-wiped and refurbished is donated to charity institutions. Any equipment that we can’t re-use in-house is recycled by professional companies. Additionally, we abide by the contract with our suppliers to return IT electronic equipment and the empty toner cartridges for recycling. As a result of these practices, during 2024, a total of 543 kg IT electronic equipment and a total of 87 toner cartridges were collected from our offices.
Marine Environment Stewardship
Conforming to Environmental Laws & Regulations
Environmental protection and pollution prevention are considered as top priority matters by all crew. In Danaos, we implement a Zero MARPOL Incident policy and any oil spill or leak is documented, reported and analyzed to ensure that similar incidents do not occur in the future.
The most common reason for spillages is the human factor, while minimizing the exposure risk associated with pollution is a challenging task. In order to mitigate the risk of an oil spill, there is a series of measures described in an action plan, such as maintenance of all critical machineries for the related operations, routine drills and simulations, training both onboard and onshore through safety meetings and a strong crisis management policy. Danaos has also developed a Safety Management System and policies that promote pollution prevention and we have taken a step further to predict and prevent any potential threats to the marine environment. Danaos is continuously operating with zero spills, reflecting the structure and the efforts of the Company.
At same time, we have established and implemented a robust Environmental Management System and our fleet systematically complies with or exceeds environmental laws and regulations as imposed by:
- IMO
- U.S. Oil Pollution Act of 1990
- CERCLA (spills and releases of hazardous substances)
- Clean Water Act
- Clean Air Act
- EU MRV regulation
In 2024 there were zero (0) cases of spills above 1bbl, while zero containers have been reported to be lost at sea.
In 2024 we had one (1) fine imposed related to the Sulphur limit of the fuel oil consumed withing Emission Control Area. The non-compliance was attributed to an inadvertent mixing of fuels. After investigation the relevant procedures were reviewed and all our crew members involved with fuel management aboard our vessels were alerted accordingly in order to prevent reoccurrence.
In Danaos an action plan described by a set of measures is in place to mitigate the risk of oil spill, such as maintenance of all critical machinery for the related operations, routine drills and simulations, training both onboard and onshore through safety meetings, and a strong crisis management policy.
Biodiversity
Protecting Marine Biodiversity
Addressing the loss of biodiversity is a critical issue, especially considering how interconnected ecosystems are with human well-being and business operations. In this context, we apply sustainable shipping practices by minimizing the environmental impact of shipping through the reduction of pollutants, such as ballast water discharge and implementing stricter waste management practices which can prevent harm to marine ecosystems. In addition, we respect Marine Protected Areas in operational routes, ensuring that critical habitats are preserved and reducing the risk of ecosystem destruction.
The strengthened policy on waste management, the monitoring of fresh water consumption, the recycling actions, recently introduced for mooring ropes on our vessels, along with company’s 3R (Repair-Reuse-Recycle) policy, the compliance with international regulation for ballast water by installing UV technology systems in all of our containerships (thus majorly avoiding discharge of chemicals from treatment) are tokens of our efforts to protect marine biodiversity. By the end of 2024, 100% of our diversified fleet of containerships and bulk carriers has been retrofitted with BWTS and we are constantly monitoring the percentage of operation of these BWTS systems in sensitive areas under MARPOL (MEPC. 1/Circ. 778). In addition, the application of sewage treatment and compliance with relevant standards, the adoption of the aforementioned “zero-spill” policy with continuous fleet monitoring and predictive maintenance are implemented and have paved the way to reach targets and set new, more ambitious ones. In Danaos we have a well-structured action plan in place for oil spill risk mitigation. Preventing and responding to such incidents is crucial, not just for environmental protection but also for ensuring the safety of crews and surrounding communities. The proactive approach through maintenance, drills, training, and crisis management policies shows a clear commitment to minimizing risk and responding effectively in the event of an emergency. We have established and implemented a robust Environmental Management System and our fleet systematically complies with or exceeds environmental laws and regulations.
Additional measures taken to address the loss of biodiversity include the application of biocide free hull coatings to some vessels, the incorporation in our online fleet monitoring of areas included in “Blue Whales Blue Skies” and “SAvE Whales” initiatives in a geofencing-like approach and raising concern to our clients with chartered vessels on complying with the voluntary speed reductions. Danaos Officers are also highly advised to report areas of encounter with cetacean and protected species.
Sustainability must be embedded across all levels— from ownership policies to individual mindsets— is key to making lasting change. When every crew member and employee understand their role and the collective responsibility, it strengthens the entire organization’s commitment to sustainability.
This is what we strive for by investing in continuous training to build awareness and encourage sustainable practices in day-to-day operations.
Additional measures taken to address the loss of biodiversity include the application of biocide free hull coatings to some vessels, the incorporation in our online fleet monitoring of areas included in “Blue Whales Blue Skies” and “SAvE Whales” initiatives in a geofencing-like approach and raising concern to our clients with chartered vessels on complying with the voluntary speed reductions.
Monitoring and Compliance in Particularly Sensitive Sea Areas
As a tonnage provider, we monitor our vessels’ trading route and trespassing (if any) in any sensitive areas and particularly sensitive areas as per MEPC.1/Circ.778/Rev.3 Annex 2, Page 1, through our online performance tools. More specifically, all Sensitive areas and Particularly Sensitive Areas have been mapped in our Waves Analytics platform and the % of time spent in PSSAs is automatically produced based on vessels’ coordinates as received from our online performance tools. In total, 1.7% of the travel time was spent in PSSAs within 2024. During this time, crew onboard strictly follows all associated protected measures as listed as in MEPC.1/Circ.778/Rev.3 Annex 2, Page 1, that include detailed reporting to the authorities, speed reduction, no anchoring, while threatening activities are avoided (i.e. no cargo loading/unloading, no bunkering, etc.).
Our operations primarily occur in international waters, which means that the standard reporting requirements typically applicable to coastal or inland activities do not directly apply to us. However, we are deeply committed to environmental stewardship and regulatory compliance. In particular, we maintain vigilant oversight in areas designated as Particularly Sensitive Areas. In these regions, our operations are strictly limited to transshipment activities only, ensuring that no cargo is loaded, unloaded, or that bunkering operations are conducted. This approach helps us prevent any potential environmental risks associated with such activities, and it demonstrates our proactive commitment to safeguarding vulnerable marine ecosystems while operating responsibly on a global scale.
It is sensible that since Danaos is not a liner company and running of the ships are in the hands of our clients, some operational measures pertain to the awareness of the charterers. Apart from, for example, voluntary speed reduction, the avoidance of illegal wildlife transport is a commitment made officially by most of our clients.
Supporting the environment is also manifested by company’s afforestation actions on an annual basis and contribution to HELMEPA (Hellenic Marine Environment Protection) initiatives through various social actions and participation.
Water Usage And Effluents Treatment
Water Used for Oceanic Operations
Danaos has comprehensive procedures in place for handling various types of water discharges, with a clear alignment to international guidelines like the IMO and local regulations. This proactive approach not only minimizes the environmental impact of our operations but also helps ensure compliance with increasingly stringent global regulations.
Given the variety of water discharges involved, it’s essential to have robust risk management tools to assess and mitigate potential impacts.
The Company’s policy concerning the prevention of pollution by sewage from its ships is based on the following principles:
- All sewage equipment on board the Company’s ships is type approved as indicated by a maker’s plate affixed to the equipment and are approved by the Flag Administration.
- Vessels equipped with sewage holding tanks should use these tanks in all ports and following MARPOL Guidelines, dispose of the contents further than 12 miles from nearest land and in accordance with the approved discharge rate.
- Treated sewage along with graywater can be temporarily disposed through Class approved piping to designated temporary holding tanks and thereafter discharged to the stringiest regulation applicable.
- Vessels equipped with chemical treatment plants should be used while in transit throughout all coastal areas.
The designated manual for the wastewater shipboard management is the Garbage & Sewage Management Plan (GSMP), which describes all the applicable International and National requirements. The manual defines the person responsible for the execution of the Sewage Management Plan, as well as best practices for the efficient running of a sewage treatment plant. Periodic maintenance and inspection records have been included into PMS.
Apart from the assigned personnel’s specific duties familiarization, all shipboard personnel are further trained and educated during the regular safety and environmental meetings held on board on the following topics:
- International (MARPOL Annex IV) and national legislation of the States/ports called.
- Specific requirements for wastewater treatment and disposal of wastewater effluents.
- The operation of wastewater treatment facilities onboard.
- The disposal of wastewater to shore facilities
- Health and sanitary considerations, best practices to avoid abnormalities to sanitary system onboard.
All commercial vessels greater than 79 feet must have a permit, such as the Vessel General Permit (VGP) before they can legally discharge graywater in US waters. Vessels cannot operate in US Waters without a VGP in place. Danaos has integrated VGP requirements for the control of graywater impacts into its DSMS covering all fleet vessels with an onboard specific manual and CBT for crew’s familiarization.
Moreover, the ESG Suppliers’ assessment program was updated to incorporate the water coverage information by adding extra field in the Danaos ESG Assessment Questionnaire, aiming to engage suppliers by addressing their water usage and effluents treatment policy implemented in 2024.
As a major container company, our impact on marine eco-systems can potentially be significant due to the ballast water quantities that are needed for vessels operation and stability. In this respect, we aim at the lowest possible impact to the marine life and in order to achieve it, we strictly follow all relevant regulations in place.
Danaos initiated Water Ballast Treatment (WBT) installation onboard vessels back in 2018. Currently, 100% of the fleet is already equipped with WBT. These are fully operational units and are used regardless of whether they have passed the IMO compliance date or not. In all our containerships, UV light is used for water sterilization, eliminating any bacteria and pathogens from the water volumes used. By the end of 2024, the last vessel had the system installed and running.
We have also adopted a Ballast Water operation policy, which prevents the transfer of harmful alien aquatic species from one region of the world to another. All engineering, plan approval and installation work has been carried out in- house by Danaos’ R&D and Technical department. Each Ballast Water Treatment System has been evaluated for its efficiency, technical competence, operational flexibility, durability and environmental friendliness, through principal certification and acceptance by the IMO, the US Environmental Protection Agency and the European Committee.
In 2024, the total volume of ballast water that was operated through BWTS in Danaos’ fleet was remarkably increased to 12,270,328 cubic meters, signifying 127% increase compared to previous year, which is due to fleet growth, as well as to the increased use of ballast water of the newly acquired bulk carriers. We should mention that we aim to optimize the use of ballast water equipment and, whenever possible, we perform ballast operations by gravity to reduce fuel consumption.
Discharged ballast water is tested on an annual basis for all Danaos vessels. Samples are tested annually regardless of VGP port calls in order to verify system operation and proper discharge properties. Within 2024, a total of 81 samples have been tested and all found within limits.
Scrubber discharge water is tested in all vessels of our fleet that are equipped with open loop scrubber. In 2024, the 6 newbuilding vessels equipped with open loop scrubber were delivered from shipyard and 2 bulk carriers recently acquired are also fitted with SOx Scrubber. As per VGP, washwater sampling from 3 positions shall take place twice during the first year of permit coverage or system operation, whichever is later. The two samples must be collected at least 14 days apart, while -as per MEPC- sampling should take place only during system testing (commissioning) and at a 12-month interval for a period of two years of operation (minimum 3 samples). Apart from the standard VGP requirement, Danaos requires that washwater is tested on an annual basis, in order to verify system operation and that the discharged water is within the permissible limits. Within 2024, a total of 10 samples have been tested and 9 found within limits. Resampling was carried out as a corrective action for the one out-of-limits test from washwater samples, to ensure proper operation of system. The resampling results were found to be within limits, too.
Though water withdrawal is not applicable for Danaos due to the nature of the company, we also monitor the total ballast water operated within each year, quantities are reported from vessels on a quarterly basis. Total ballast treated within 2024 is 12,270,328 m³; total ballast quantity is also related to the total number of vessels of the fleet and the diversification of the fleet and is expected to increase along with the fleet growth.
Fresh Water Use
Since fresh water is becoming extremely scarce throughout the years, monitoring of freshwater consumption can promote our company’s competitiveness through cost savings and reduced environmental liabilities, while also allowing us to be prepared for potential future environmental regulations.
Water consumed in headquarters is monitored from 2023 and, as of 2024, we have been monitoring the water withdrawals from all Offices. The water consumed in our headquarters during 2024 was 813 m3, showing an increase in relation to 2023 due to the company’s growth and personnel increase. In case of water consumed in company’s premises, the effluent is discharged in the public wastewater drainage systems according to the local legislation and specifications.
As far as our vessels are concerned, 17,591 MT of fresh water have been received onboard. This is a small fraction of the fresh water that is used on board, given that the vast majority of volumes consumed are generated by sea water with desalination units. Total consumption is linked with the number of vessels and, since the fleet is growing, the total fresh water supplied will increase respectively.
Monitoring is carried out on a quarterly basis by our SQE department, where vessels report relevant consumption per category and we have also included a daily average FW consumption in our monitoring scheme.
Moreover, Danaos conducts onboard fresh water analysis in order to confirm that fresh water meets specific standards as per MLC 2006. The Maritime Labour Convention (MLC 2006), which came into force on August 20, 2013, demands that Potable (Drinking) Water should be tested (in accordance with World Health Organization guidelines for drinking water quality) at least once, at intervals of not more than six (6) months. Every vessel sends 2 samples on an annual basis, usually 1 sample from ER fountain and another from galley or accommodation areas, in order to ensure that water quality meets WHO standards in all locations. Within 2024, a total 166 samples were sent for analysis and 152 were found within limits. Resampling has been carried out as corrective action related to out-of-limits test results from freshwater samples to ensure compliance and the resampling results provided until the day this report was being prepared have been found within limits. Only four tests remaining in progress. We have a dedicated contact with a laboratory in order for the whole testing process to run smoothly and avoid unnecessary delays of the analysis results.
EU Projects
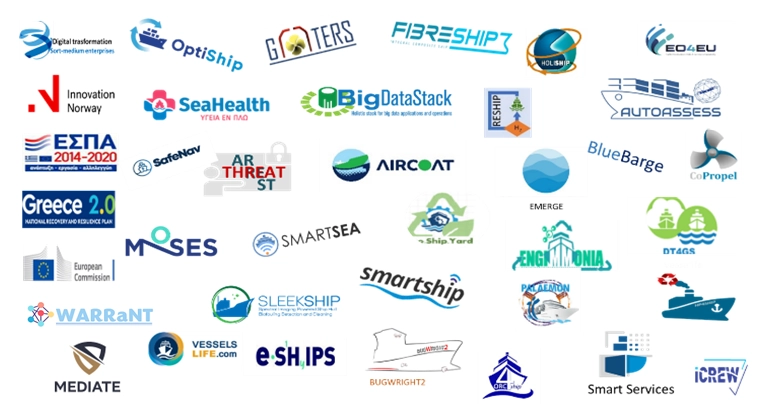
2024 EU Projects
New EU Projects
As we enter 2025, Danaos Research Center’s portfolio is enriched with three winning proposals, each awarded EU funding for a three-year duration. These projects—D-Navio, Mediate and Warrant— represent significant advancements in the maritime industry. They incorporate cutting-edge technologies, such as AI Digital Twin, Zero-Trust principles, IoT, Federated Learning and MCDA, which will be central to new innovative approaches to improve security, safety and operational efficiency.
These initiatives not only highlight our commitment to advancing research and development in the maritime sector but also demonstrate our dedication to fostering innovation and contributing to the future of maritime technology and sustainability and Secured Digital Transformation.
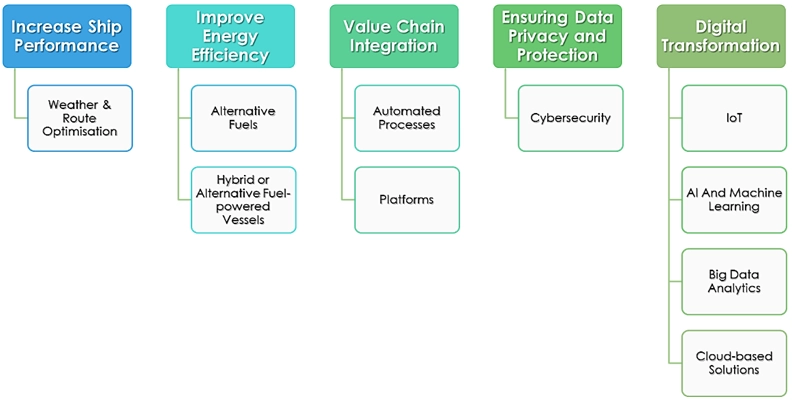
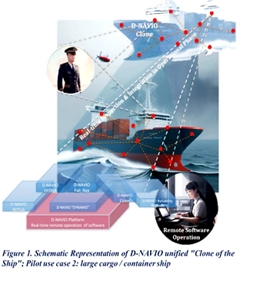
D-Navio
This project focuses on developing a next-generation digital twin for large ships through the Intelligent Digital Twin (IDT) system. Its innovative approach aims to enhance maritime safety, improve environmental efficiency and facilitate the transition to autonomous vessels. By integrating explainable AI, self-healing technologies and interdisciplinary knowledge, D-NAVIO will revolutionize risk assessment and hazard management in maritime operations, setting new standards in the field.
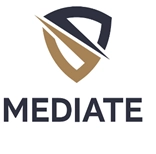
Mediate
MEDIATE is a research program dedicated to addressing the security and privacy challenges within the computing continuum, focusing on the integration of cloud, edge and Internet of Things (IoT) systems. With this project, we aim to develop a robust technology based on zero-trust principles and federated learning to enhance cybersecurity resilience, mitigate vulnerabilities and ensure secure integration across these complex systems. This will position us at the forefront of cybersecurity innovation, enabling more secure, privacy-conscious and resilient digital ecosystems across industries.
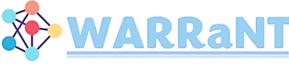
WaRRaNT
WaRRaNT The WARRaNT project is set to address the challenge of enhancing the dependability, safety, security and resilience of Waterborne Digital Systems (WDS) and digitalized ships. Through its cutting- edge solutions, Danaos anticipates significant advancements in real-time monitoring, predictive maintenance and risk management, ultimately enabling safer, more resilient and autonomous maritime operations. This will have a lasting impact on improving operational efficiency, reducing risks and fostering industry-wide adoption of best practices from safety-critical sectors.
Innovation and Digitalization
Shipping companies are continuously seeking ways to adopt new technologies and enhance the efficiency of their investments. As global supply chains demand a smooth flow of goods and services, Digital Business has become a crucial enabler for shipping companies. Modern technologies, such as the Internet of Things (IoT), Big Data, Artificial Intelligence (AI), Application Programming Interfaces (APIs) and sensors, along with large volumes of data, are being harnessed to optimize operations, boost efficiency and lower costs. In order all of these to be implemented, changes in the operating models are required as soon as possible in order for the whole industry to adapt to the new demanding reality.
Our target is to work on the full digitalization of company’s processes ensuring close control and prompt response, promoting fuel efficiency. Online systems installation further increased within 2024, with 4 additional vessels from the existing container fleet, as well as the 6 newbuilding vessels delivered within 2024, leading to a total of 70 out of 71 container vessels equipped with high frequency data (98.6% of the container fleet). Another 7 installations were completed on the bulk fleet and 5 more installations are planned for 2025 (3 on existing bulk carrier vessels and another 2 on the newbuildings that will be delivered next year). Within 2024, we introduced our internal ETS EUAs calculation tool in the Waves Data Analytics platform, automating CO2 emissions reporting, in order to comply with EU Emissions Trading System (ETS) regulations and provide our charterers with billing accuracy.
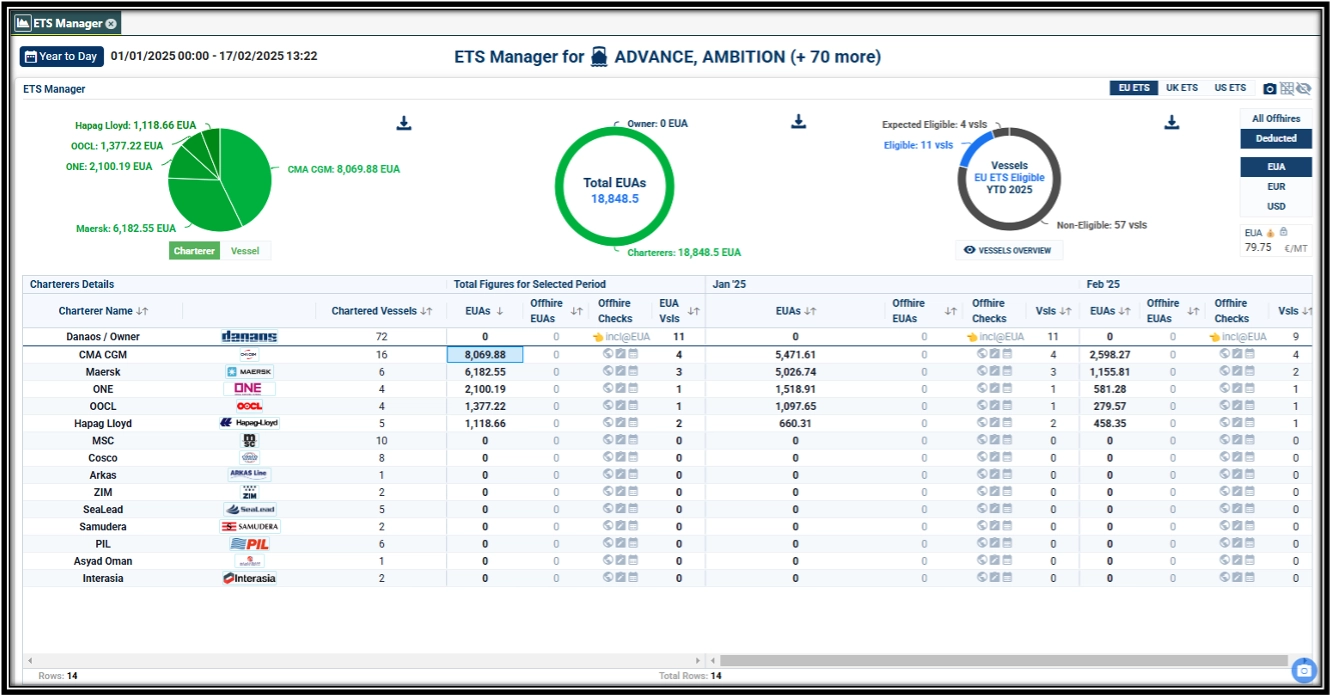
In 2024, spatio-temporal applications have been also integrated in the Waves system, including IBF/ITF War Zones to monitor high-risk areas, calculating potential extra compensation or benefits for the crew and offering real-time insights into high-risk areas. Moreover, we have been monitoring through our Waves system the vessels’ routes to ensure compliance with environmental protections and speed limitations in areas designated as “Whales Initiatives”, such as Blue Whales Blue Skies Zones, Vancouver Killer Whales Zone, NOAA Right Whale Ship Strike Reduction Rule Zones and SaVE WHALES Zones (Kythira). The above is an innovative and impactful application, which serves two important functions: safety for vessels and protection for marine life -whales in particular-, reflecting a combination of navigation technology and environmental responsibility.
The vessels’ performance analysis was further digitized within 2024 in Waves “Spot inspector” by applying multi-criteria filtering, regression analysis and post-cleaning event comparisons to detect anomalies and maintenance needs. The analysis includes the uniformed performance evaluation of vessels, utilizing multi-criteria filtering techniques to ensure data accuracy. Regression analysis incorporating multiple models is performed to identify key relationships within the data. Additionally, outlier filtering is applied to maintain data integrity, while enabling users to effectively detect anomalies and maintenance needs. This approach also helps in assessing investments and providing valuable insights by identifying performance degradation early for future planning.
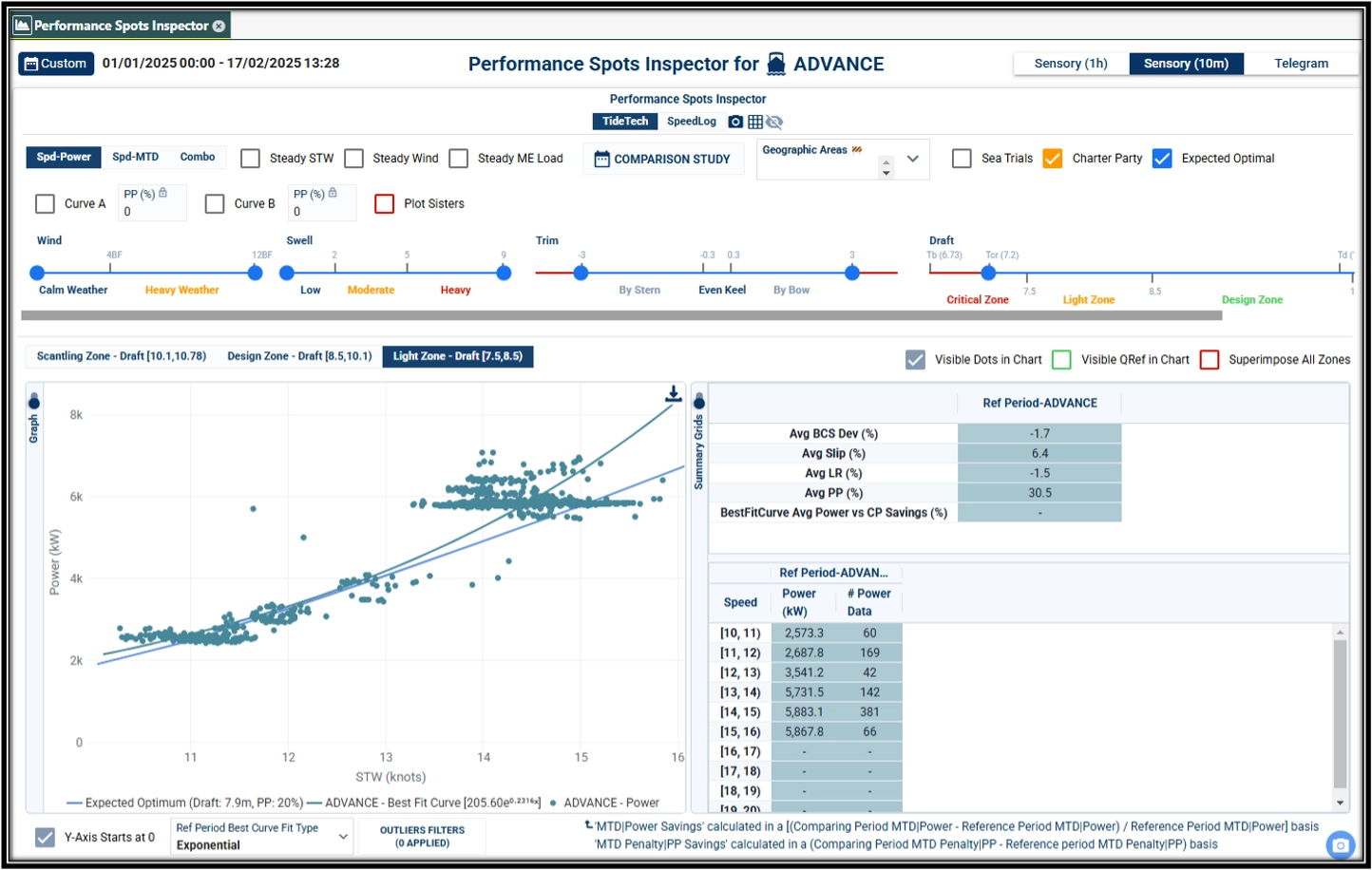
The major Waves system updates include among others operational processes, such as Port activities and Disbursement accounts, providing centralized access to invoices and documents for better cost control, as well as internal processes incorporated in Waves Data Analytics, such as Milestones Scheduler and Employees Allocation applications, which improve coordination and communication.
Moreover, crewing management is a crucial aspect of effective operations, playing a vital role in ensuring sustainable development. Danaos has enriched Crewing application into Waves Data analytics platform to digitalize the constant monitoring of onboard crew composition and ensuring compliance with regulations for crew welfare and MLC, as well as compliance with company policies. The following applications have been incorporated in Waves Data Analytics platform: Crew Payable days, Crew Allotments, Crew Working hours, Crew Contracts generator, Crew List Company Policy Violations, Crew Standard Synthesis coverage.
In Danaos, we value data sharing and transparency. Our Waves platform is being constantly upgraded to incorporate all latest regulatory affairs and technology insights, providing reliable and stable data on a real time basis. Apart for enhancing our “digital surveys” in the performance of our vessels, we have participated in client initiatives for development of their in-house tools for the same purposes, enabling benchmarking and cross-validation of data gathered from both sides. This healthy collaboration will drive shipping into decarbonization, overcoming competition and commercial barriers.